In the world of pharmaceutical manufacturing, particularly in the production of Active Pharmaceutical Ingredients (APIs), cleanroom environments are critical. These controlled spaces demand stringent standards to ensure product quality and worker safety. Among these standards, cleanroom lighting plays a pivotal role. This blog explores the key aspects of cleanroom lighting standards for API production.
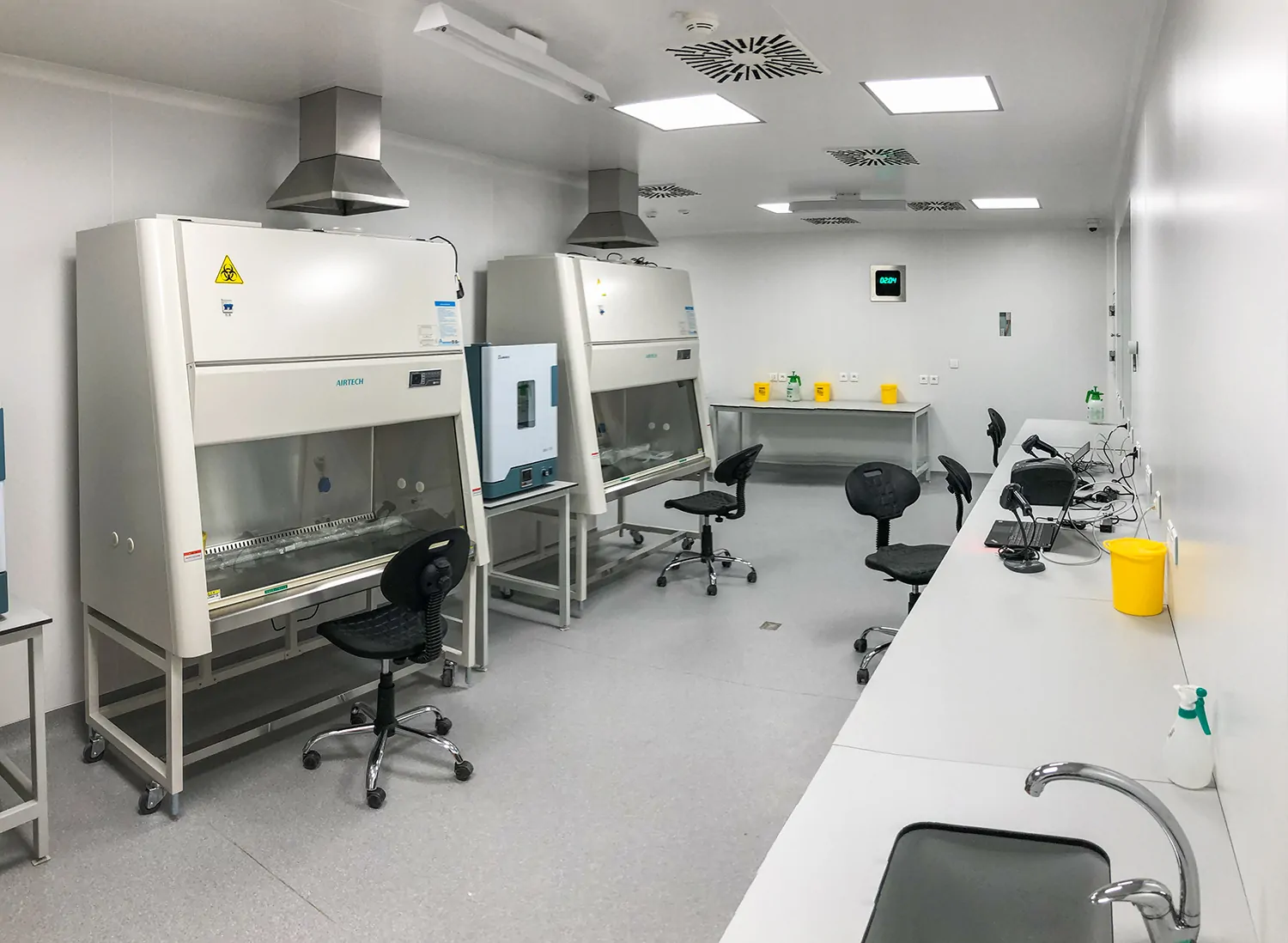
Importance of Proper Lighting in Cleanrooms
Effective lighting in cleanrooms is essential for several reasons:
Quality Control:
Adequate lighting ensures that workers can accurately perform tasks such as inspection and assembly, reducing the risk of errors.
Safety:
Proper lighting helps maintain a safe working environment by preventing accidents and ensuring clear visibility. Compliance: Adherence to lighting standards is often a regulatory requirement, ensuring that manufacturing processes meet the necessary guidelines.
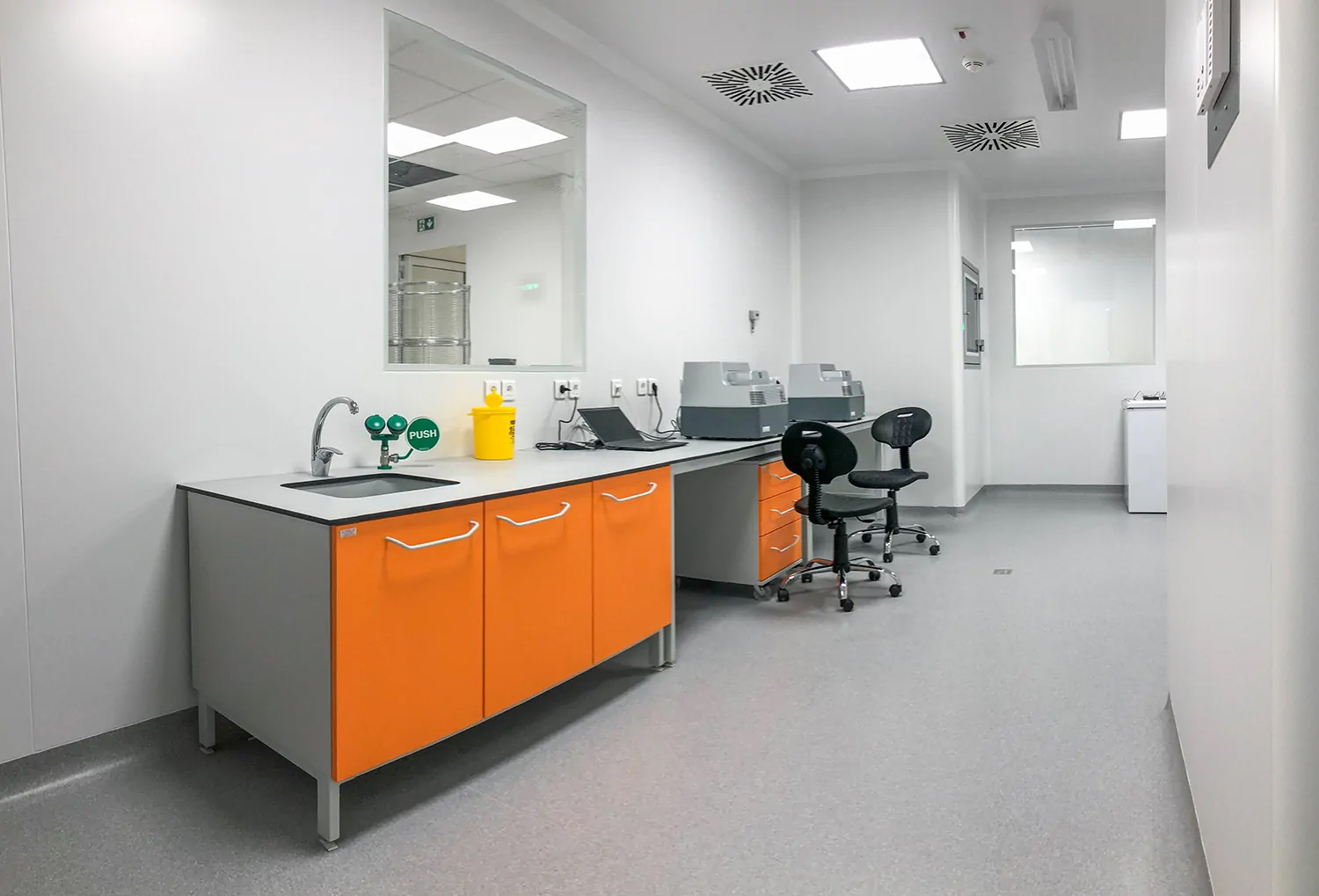
Key Lighting Standards and Guidelines
1. Intensity of Lighting
The recommended lighting levels for cleanrooms typically range from 500 to 750 lux, depending on the specific activities performed. For critical tasks requiring high precision, higher lighting levels may be necessary. Consistent and adequate lighting helps in minimizing mistakes and enhancing productivity.
2. Color Temperature
The color temperature of lighting in cleanrooms is another crucial factor. Cool white light, with a color temperature between 4000K and 6500K, is recommended. This type of light provides better visibility and reduces eye strain, which is vital for tasks requiring prolonged focus.
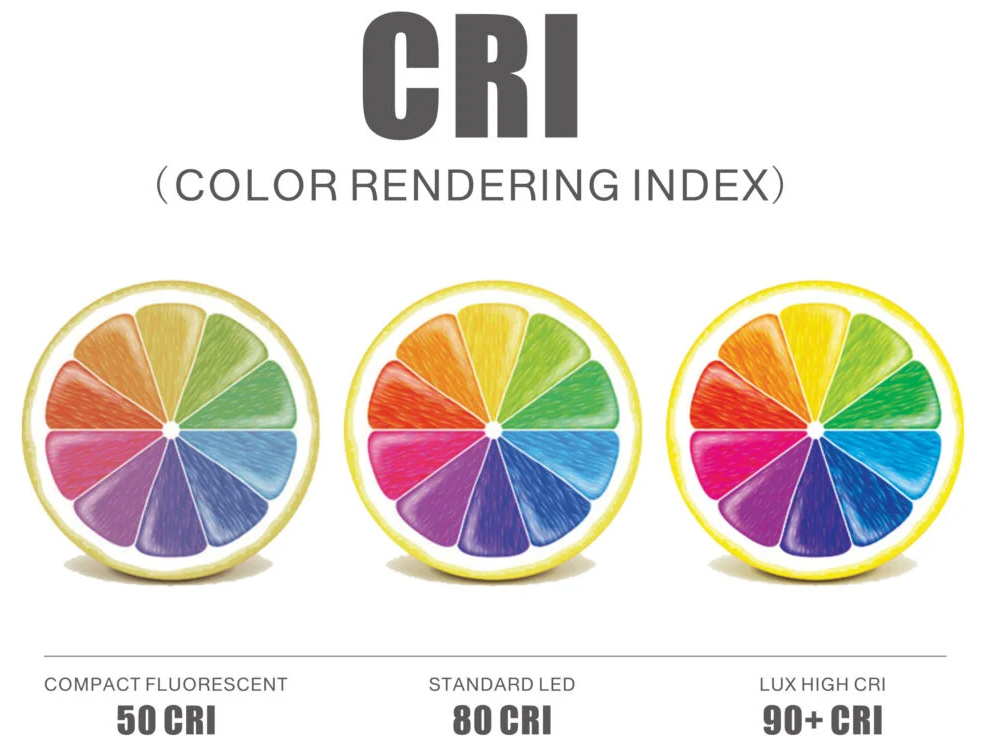
3. Color Rendering Index (CRI)
A high Color Rendering Index (CRI) of over 80 is essential in cleanrooms. A high CRI ensures accurate color differentiation, which is critical for identifying substances and conducting quality inspections. Poor color rendering can lead to misidentification and errors in the manufacturing process.
4. Lighting Control and Monitoring
Advanced lighting control systems are necessary to maintain consistent lighting levels throughout the cleanroom. These systems should allow for adjustments in intensity and automate lighting to ensure uniform illumination across all areas. Such control systems enhance energy efficiency and ensure optimal lighting conditions at all times.
5. Minimizing UV and IR Radiation
Lighting fixtures should be designed to minimize UV and IR radiation, as these can degrade pharmaceutical products. LED lighting is ideal for cleanrooms due to its low heat emission and minimal UV output. This reduces the risk of product contamination and degradation.
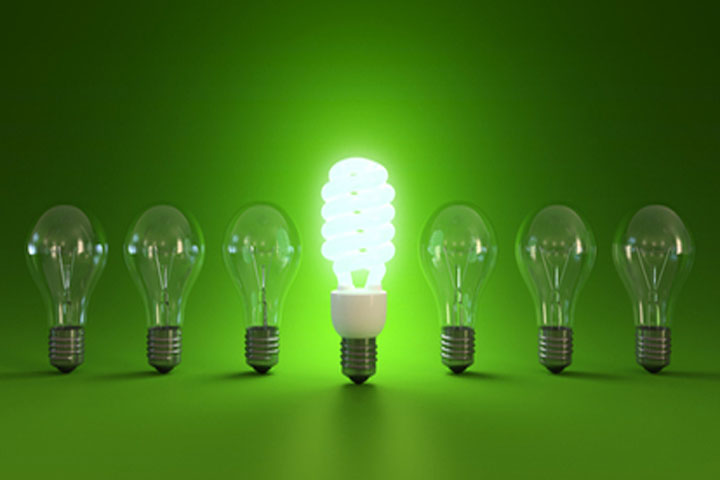
6. Types of Lighting
LED lighting is preferred in cleanrooms for several reasons:
Energy Efficiency: LEDs consume less power and have a longer lifespan compared to traditional lighting.
Low Heat Emission: This reduces the load on air conditioning systems and maintains the cleanroom environment.
Minimal UV Emission:Ensuring that products are not exposed to harmful UV rays. Fluorescent lights may also be used, provided they are equipped with appropriate UV filters.
7. Cleanability and Contamination Resistance
Lighting fixtures in cleanrooms must be designed to resist contamination and be easy to clean. Smooth surfaces and sealed enclosures prevent dust and particle accumulation. The fixtures should also withstand regular cleaning with chemicals used in maintaining cleanroom hygiene.
8. Regulatory Standards
Several international standards and guidelines govern cleanroom lighting:
ISO 14644-1: Specifies the classification of air cleanliness by particle concentration, which indirectly affects lighting requirements.
GMP (Good Manufacturing Practice): Includes guidelines for the design and maintenance of cleanrooms, encompassing lighting standards.
EN 12464-1: Provides standards for lighting of indoor workplaces, applicable to cleanrooms.
9. Ergonomics and Worker Comfort
Beyond technical specifications, ergonomics play a crucial role in cleanroom lighting. Properly designed lighting reduces eye strain and fatigue, enhancing worker comfort and productivity. Adjustable lighting levels and well-distributed light prevent shadows and glare, creating an optimal working environment.
Conclusion
Proper lighting design in cleanrooms for API production is essential for ensuring product quality, worker safety, and regulatory compliance. By adhering to established standards and leveraging advanced lighting technologies, manufacturers can create efficient, safe, and productive cleanroom environments. Implementing these standards not only enhances operational efficiency but also ensures that the pharmaceutical products meet the highest quality standards.