The world of manufacturing is changing faster than ever, and at the heart of this transformation is Industry 4.0—a term that might sound futuristic but is already reshaping how we produce, manage, and think about goods. It’s not just about machines and data; it’s about people, collaboration, and creating smarter, more efficient ways to work. In this blog, let’s explore how Industry 4.0 is redefining production management in the digital era and what it means for the humans behind the machines.
What is Industry 4.0, Really?
Industry 4.0 is often described as the fourth industrial revolution, but what does that mean in plain terms? It’s about bringing together cutting-edge technologies like the Internet of Things (IoT), artificial intelligence (AI), big data, and cloud computing to create smarter, more connected factories. Imagine machines that can “talk” to each other, systems that predict problems before they happen, and production lines that adapt on the fly. It’s not just about automation—it’s about creating a seamless partnership between humans and technology.
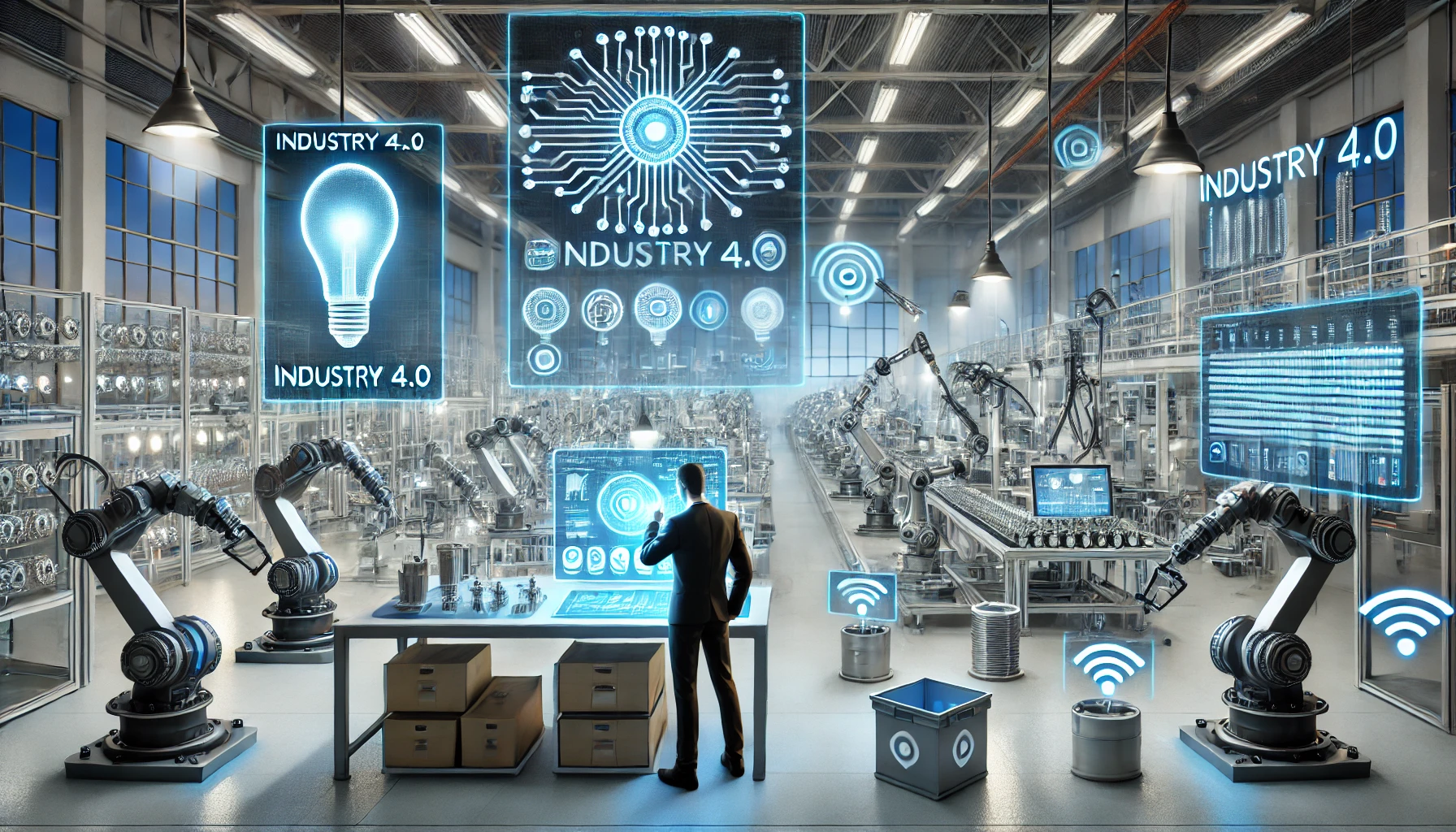
The Human Side of Smart Factories
When we talk about smart factories, it’s easy to picture rows of robots working tirelessly. But behind every machine is a team of people designing, monitoring, and improving the process. Smart factories empower workers by giving them real-time insights into production. For example, instead of manually checking equipment for wear and tear, sensors can alert workers when maintenance is needed. This means less guesswork, fewer breakdowns, and more time for employees to focus on creative problem-solving and innovation.
Real-Time Data: A Game-Changer for Decision-Making
In the past, production managers had to rely on historical data and gut feelings to make decisions. Today, Industry 4.0 puts real-time data at their fingertips. Imagine being able to see exactly how much energy a machine is using, how quickly a product is moving through the line, or where a bottleneck is forming—all in real-time. This isn’t just about efficiency; it’s about giving people the tools they need to make smarter, faster decisions that keep production running smoothly.
Predictive Maintenance: Saving Time and Stress
Let’s face it—equipment breakdowns are a headache. They disrupt schedules, cost money, and create stress for everyone involved. Industry 4.0 introduces predictive maintenance, which uses sensors and AI to monitor equipment health and predict when something might go wrong. Instead of waiting for a machine to break down, maintenance can be scheduled proactively. This not only saves time and money but also reduces the stress of unexpected downtime, allowing teams to focus on their work without constant worry.
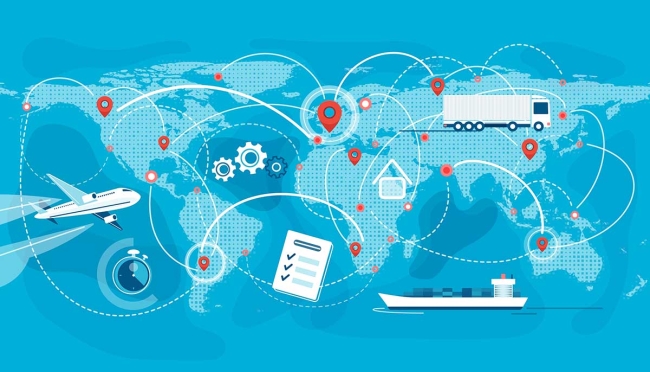
A More Connected Supply Chain
In the digital era, production management isn’t just about what happens inside the factory—it’s about the entire supply chain. Industry 4.0 enables seamless communication between suppliers, manufacturers, and customers. For example, if a supplier is running late, the factory can adjust its schedule in real-time to avoid delays. This level of collaboration makes the supply chain more resilient and responsive, which ultimately benefits everyone involved, from the factory floor to the end customer.
Customization Without Compromise
One of the most exciting aspects of Industry 4.0 is its ability to balance customization with efficiency. In the past, producing customized products often meant slowing down the production line. Today, advanced robotics and AI-driven systems can adapt quickly to new requirements, allowing manufacturers to offer personalized products without sacrificing speed or quality. This means happier customers and more opportunities for businesses to stand out in a competitive market.
More Than Just Numbers
The advantages of Industry 4.0 go beyond cold, hard statistics. Sure, it leads to increased efficiency, cost savings, and higher-quality products, but it also creates a better work environment. Employees spend less time on repetitive tasks and more time on meaningful work. Factories become safer, more sustainable, and more enjoyable places to work. And let’s not forget the environmental benefits—optimized resource usage and reduced waste mean a smaller carbon footprint for the planet.
It’s Not All Smooth Sailing
Of course, adopting Industry 4.0 isn’t without its challenges. Upgrading to smart technologies requires significant investment, and integrating new systems with existing ones can be complex. There’s also the need for training—workers need to learn how to use these new tools effectively. And with increased connectivity comes the risk of cyber threats, so robust cybersecurity measures are essential to protect sensitive data and keep operations running smoothly.
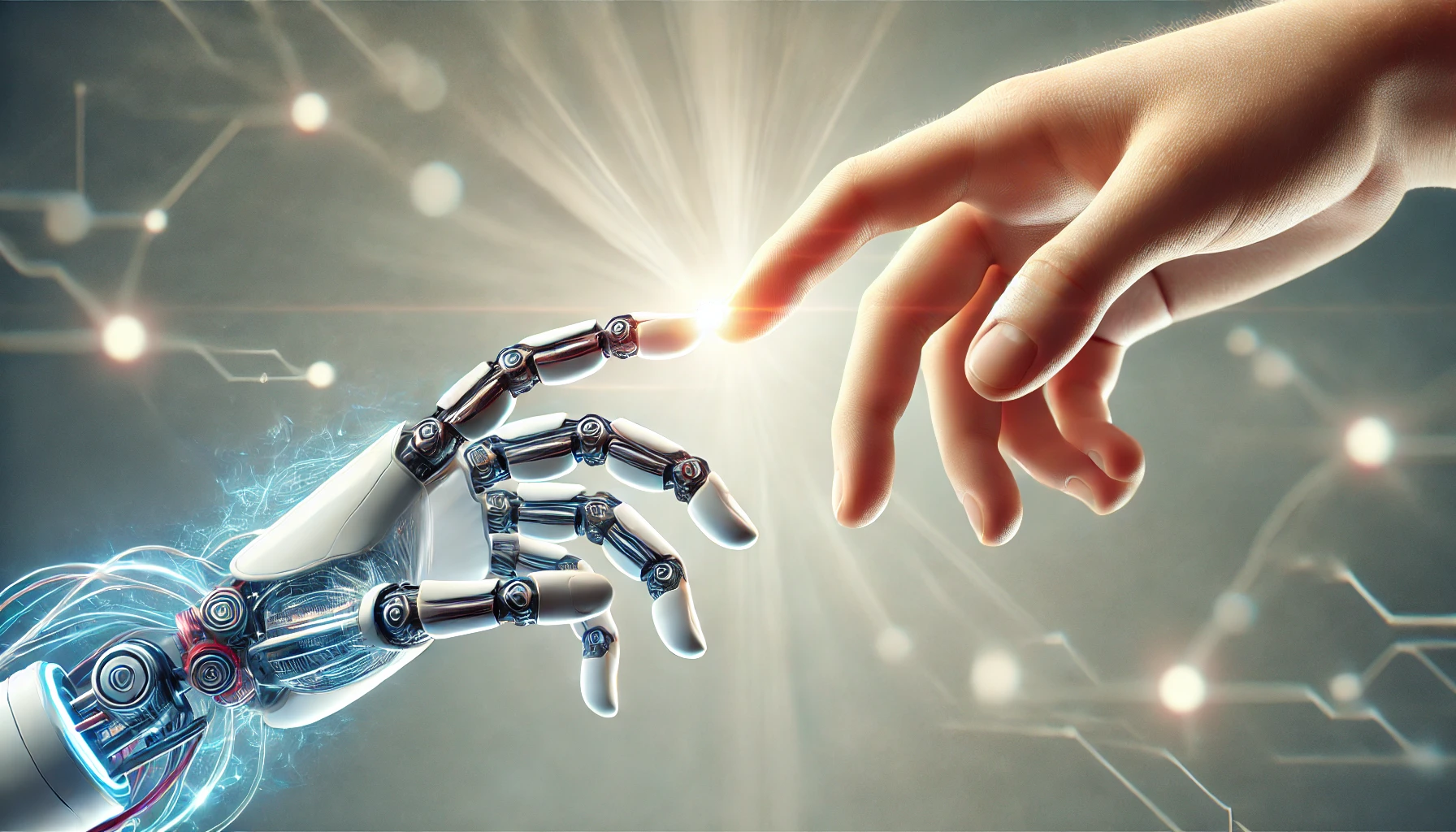
A Partnership Between Humans and Machines
As we look to the future, Industry 4.0 will continue to evolve, but one thing is clear: humans will always be at the center of it all. Advances in AI, machine learning, and blockchain will make production management even more efficient, but it’s the creativity, problem-solving, and collaboration of people that will drive true innovation. The factories of the future won’t just be smart—they’ll be human-centric, designed to empower workers and create value for everyone involved.

Embracing the Digital Era Together
Industry 4.0 isn’t just a technological shift-it’s a cultural one. It’s about reimagining how we work, collaborate, and create in the digital era. By embracing these changes, manufacturers can unlock new levels of efficiency, flexibility, and sustainability. But more importantly, they can create a future where technology enhances human potential, rather than replacing it. The journey to Industry 4.0 is just beginning, and it’s one we’re all taking together-machines and humans, side by side.